An Introduction to Corrosion and Its Challenges
The annual cost of corrosion is estimated to be 2.5 trillion dollars globally, accounting for over 3% of the global GDP. High-performance coatings are crucial in anti-corrosion efforts and in extending the life of metal resources across various sectors, including transportation, utilities, manufacturing, and national defense. As such, protective coatings play a vital role in the global migration to sustainable living.
Corrosion protection is achieved through the application of a high-performance, multi-coat coatings system, primarily comprised of a base coat that has heavy-metal corrosion inhibitors. Corrosion inhibitors are additives that, when applied in small amounts to a hostile environment, reduce the rate of attack on a material (corrosion rate) such as a metal. Regulations around heavy-metal corrosion inhibitors continue to be more complex and restrictive each year in order to reduce heavy-metal chemistries and force manufacturers to innovate to replace toxic substances.
Historical use of corrosion inhibitors based on chromium, lead, and zinc chemistries has brought great benefit to coating performance, but at a detriment to the environment and human health. The below table summarizes the heavy-metal corrosion chemistries of chromium, lead, and zinc:
Heavy-metal type | Chemical element | Key information |
Lead | 82 Pb 207.2 | – Banned in the United States in the early 1970s. Causes cardiovascular disease, infertility, cognitive impairment, and death. – 900,000 annual deaths despite regulations in 87 countries. – The UN Lead Paint Alliance was created to reduce the use of lead-based paints; it continues its focus on 100+ nations. |
Chromium | 24 Cr 52.0 | – Known carcinogen, aquatic toxin, and reproductive disrupter. – Continues to be used in high performance applications, such as aerospace. – 2019 sunset date for use in the EU without special authorization. – Substance of Very High Concern. |
Zinc | 30 Zn 65.4 | – Chronic aquatic toxin. – Candidate List of Substances of Very High Concern (SVHC) for Authorization. – GHS hazard labeling is required for any formulation of more than 0.25%. – Less severe in comparison to Lead and Chromium, but will also very likely be banned. |
These lead, chromium, and zinc examples are merely a glimpse into the complex global regulatory environment that coatings manufacturers must consider when designing, producing, and selling products. The complexity of regulatory compliance continues to grow as countries establish their regulatory limitations for each of these elements. To achieve optimal corrosion inhibition, transitioning to heavy-metal-free inhibitors in water-based systems will ease the navigation of complex regulatory scrutiny. Technological advances have already produced alternatives containing no heavy metals that maintain coating performance.
Inorganic and Organic Corrosion Inhibitors
Both inorganic and organic compounds can achieve corrosion inhibition. These compounds work by forming a protective layer on the metal surface, thereby slowing down or preventing the electrochemical reactions that cause corrosion.
Inorganic inhibitors
Inorganic inhibitors are typically compounds containing elements such as metal salts, oxides, phosphates, and silicates and are known for their stability and resistance to high temperatures. Anodic and cathodic inhibitors target different parts of the corrosion process – anodes are where oxidation occurs and cathodes are where reduction occurs. As shown in the image below, anodic inhibitors inhibit the anode’s oxidation process by forming a protective film on the metal’s surface. This film acts as a barrier that shields the metal from the corrosive environment. On the other hand, cathodic inhibitors work by inhibiting the reduction reactions at the cathode through the consumption of electrons and the reduction of oxygen or other species. By hindering the cathodic reactions, cathodic inhibitors help slow the overall corrosion process.
Source: REDA Water
Organic inhibitors
Organic inhibitors are composed of carbon and hydrogen atoms. The image below shows that organic inhibitors are generally organic compounds containing polar functional groups that adsorb onto the metal surface and create a protective layer. These inhibitors reduce the rate of anodic or cathodic reactions contributing to corrosion. Organic corrosion inhibitors are generally heavy-metal free and more environmentally friendly, which has generated increased interest and use in protective coatings.
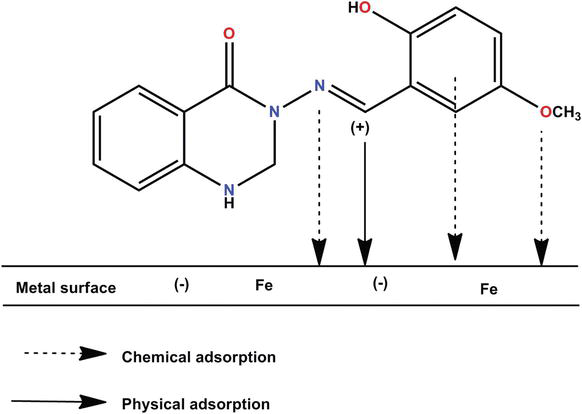
Source: Corrosion Inhibitor, Principles and Recent Applications
In some cases, a combination of both inorganic and organic inhibitors, known as synergistic inhibitors, can provide enhanced protection. This approach capitalizes on the strengths of both types of inhibitors. The choice between these compounds depends on factors such as the type of metal substrate, the corrosive environment, cost considerations, and regulatory requirements involved. The recommended range of usage of the two is formulation dependent as well.
According to researchers at ICL Phosphate Specialty, the total formula weight or composition can be used as a baseline for determining inorganic and organic dosage amounts. Typically, inorganic compounds comprise 3-10% of the total formula weight, while organic compounds have slightly lower dosing, comprising 1-3% of the total formula weight. However, it is difficult to state that the inhibitors will always fall in a specific range, as factors such as the coating technology, pigments, and other additives will impact and shape the final formulation build.
Combining inorganic and organic chemistry types can provide superior performance for corrosion inhibition, which is particularly important as the coatings industry moves away from lead and chromium chemistries and towards heavy-metal free inorganic and organic compounds. When creating coatings solutions, researchers can consider the following:
Consideration | Details |
Combining the inhibitors | Utilize the synergy of multiple mechanisms to achieve the desired performance, such as inorganic and flash rust, inorganic and inorganic, and inorganic and organic. |
Optimizing the solubility of the inhibitor | Synergize the short-term and long-term corrosion inhibitors based on their solubility. |
Inhibitor concentration | Avoid direct weight-to-weight replacements. It’s more beneficial to optimize the usage level. |
Substrate specificity | Corrosion inhibitor selection can be substrate dependent. |
The Movement Towards Greener Solutions
Metal asset protection is an essential part of the global economy, given the resource’s prevalence in a wide variety of industries. High-performing coating applications will continue to require superior protection and environmentally friendly solutions. The migration to heavy-metal free inhibitors and water-based coatings is already in progress and will only continue to grow as the regulatory landscape of the coatings industry becomes more restrictive. These green products have proven the ability to match the performance of previous solvent-borne technology, maintaining service life and the cost expectation for reapplication.
Additional Resources
- Corrosion Control: Corrosion Costs
- Science Direct: Corrosion Inhibitors
- UN environment programme: Inside the push to eliminate lead from paint
- Advancing Sustainable Water-Based Coatings with Heavy-Metal Free Corrosion Inhibitors, Michelle Bauer